
- Home
- Products
SIP Mould Reed Switch Series
When a magnet or coil creates a magnetic field that acts on the switch, both reeds of the reed switch become magnetized. An N pole is formed on the contact point of one of the reeds, and an S pole is formed on the contact point of the other reed. If the attractive force of the generated magnetic field causes the contacts to conduct, the circuit is closed. Once the magnetic field weakens to a certain extent, the reeds will separate again due to elastic force, which means the circuit is disconnected.
Line Mould Reed Switch
When a magnet or coil creates a magnetic field that acts on the switch, both reeds of the reed switch become magnetized. An N pole is formed on the contact point of one of the reeds, and an S pole is formed on the contact point of the other reed. If the attractive force of the generated magnetic field causes the contacts to conduct, the circuit is closed. Once the magnetic field weakens to a certain extent, the reeds will separate again due to elastic force, which means the circuit is disconnected.
SMD Mould Reed Switch Series
When a magnet or coil creates a magnetic field that acts on the switch, both reeds of the reed switch become magnetized. An N pole is formed on the contact point of one of the reeds, and an S pole is formed on the contact point of the other reed. If the attractive force of the generated magnetic field causes the contacts to conduct, the circuit is closed. Once the magnetic field weakens to a certain extent, the reeds will separate again due to elastic force, which means the circuit is disconnected.
Reed Relay
A reed relay is a relay that uses a coil to generate a magnetic field to actuate a reed tube. It is a coil sensing device. Therefore, the characteristics of reed relays are small size, light weight, fast response speed, short bounce time and other characteristics. Mainly used in measurement equipment, communication equipment, security equipment, medical equipment, etc.
Industrial Relay
The main function of the relay is amplification. With a very small current, a circuit with a large power can be controlled, and the control range can also be expanded. When the signal reaches a certain value, the contacts can be switched simultaneously according to different forms of the contact group. Open and connect multiple circuits to achieve the purpose of automatic switching.
Magnetic Reed Type
Proximity switch/proximity sensors are widely used in various household appliances, security systems, access control systems, safety interlocks, position positioning, and equipment automation.
Hall Type
Hall type proximity switch is composed of a reed switch and a permanent magnet. They are individually enclosed in a plastic housing for protection and ease of installation.
SCR/MOSFET Type
Magnetic Door Type
Proximity switches/proximity sensors are widely used in various household appliances, security systems, access control systems, safety interlocks, position positioning, and equipment automation.
Photoelectric Type
Inductive Type
Proximity switches/proximity sensors are therefore widely used in various household appliances, security systems, access control systems, safety interlocks, position positioning, and equipment automation.
Dual-stable reed switch
Plastic Materials
Widely used in the control of water tanks, compressors and pumps, household appliances, medical equipment, industrial braking, petrochemicals, food processing, electric power, public works, vehicles and ships, etc.
Stainless Steel Series
Widely used in the control of Water Tanks, Compressors and Pumps, Household Appliances, Industry Automation, Medical Equipment, Petrochemical Industry, Power, Food Processing, Public Engineering, Vehicles and Ships etc.
Photoelectric Liquid Level Sensor
FAST can provide customized wide-range sensors with up to 7 set points and lengths from 20mm to 2m. The valve stem and float can be made of stainless steel, PP, NBR and other materials.
Probe Level Sensor
Continuous Resistance Change
Widely used in the control of water tanks, compressors and pumps, household appliances, medical equipment, industrial automation, petrochemicals, food processing, electricity, public works, vehicles and ships, etc.
4-20mA Current output
Widely used in the control of water tanks, compressors and pumps, household appliances, medical equipment, industrial automation, petrochemicals, food processing, electricity, public works, vehicles and ships, etc.
0-5V Voltage output
Widely used in the control of water tanks, compressors and pumps, household appliances, medical equipment, industrial automation, petrochemicals, food processing, electricity, public works, vehicles and ships, etc.
Plastic Flow Switch
All FAST flow sensors and flow switches are made of high-quality corrosion-resistant materials to ensure good performance in harsh environments. They are made from materials ranging from stainless steel to engineering plastics and are highly chemically compatible.
Stainless Steel Flow Switch
FAST flow sensors and flow switches are commonly used in applications such as rotating equipment, conveyors, gas sampling and distillation, water purification systems, welding machines, semiconductor equipment, chemical processing, machine tools and robotics.
Brass Flow Switch
Gas/Air Flow Switch
Plastic Flow Sensor
FAST flow sensors and flow switches are commonly used in applications such as rotating equipment, conveyors, gas sampling and distillation, water purification systems, welding machines, semiconductor equipment, chemical processing, machine tools and robotics.
Stainless Steel Flow Sensor
All FAST flow sensors and flow switches are made of high-quality corrosion-resistant materials to ensure good performance in harsh environments. They are made from materials ranging from stainless steel to engineering plastics and are highly chemically compatible.
Brass Flow Sensor
Gas/Air Flow Sensor
Plastic Pressure Switch
When the pressure in the system is higher or lower than the rated safety pressure, the disc in the sensor moves instantaneously, and the switch joint is turned on or off through the connecting rod. When the pressure drops or rises to the rated recovery value, The disc instantly resets and the switch automatically resets, or simply put, when the measured pressure exceeds the rated value, the free end of the elastic element is displaced, pushing the switch element directly or after comparison, changing the on-off state of the switch element, to achieve The purpose of controlling the measured pressure.
Brass Pressure Switch
Stainless Steel Pressure Switch
When the pressure in the system is higher or lower than the rated safety pressure, the disc in the sensor moves instantaneously, and the switch connector is pushed on or off through the connecting guide rod. When the pressure drops to or rises to the rated recovery value, the disc resets instantly and the switch resets automatically. In simple terms, when the measured pressure exceeds the rated value, the free end of the elastic element is displaced, and the switch element is pushed directly or after comparison, changing the on-off state of the switch element to achieve the purpose of controlling the measured pressure.
Pressure Sensor
Probe Water Leak Detection Sensor
When a water leak occurs in a facility or equipment and water contacts both electrodes of the sensor at the same time, it will trigger the relay in the sensor to work and control the external alarm or water pump, solenoid valve and other equipment connected to it.
Photoelectric Water Leak Sensor
Temperature switch sensor
Temperature Sensor NTC
Temperature sensor products have stable performance, reliability and long life;NTC uses a temperature chip with a curve β value of ±1% and a resistance R value accuracy of ±1%. The outer casing is made of stainless steel 304 or nickel-plated copper, and is encapsulated with high-temperature epoxy resin. It can operate in harsh industrial environments;
Temperature Sensor-PT100
Reed Type Cylinder Magnetic Sensor
A variety of specifications are available, excellent material is wear-resistant, corrosion-resistant, not easy to damage, and long-lasting
Hall Type Cylinder Magnetic Sensor
COTO RI
The advantages of compact structure, light weight, fast response time, long life and low cost. They are widely used in household appliances, industrial products, medical equipment, toys, fitness equipment, security, intelligent control, reed relays and other devices.
COMUS GC
Reed switches have contact types of normally open (Form A), normally closed (Form B) and normally closed normally open conversion (Form C). They are triggered by the magnetic field generated by a permanent magnet or a current-carrying coil.
STANDEX ORD
Reed switch consists of an elastic reed of magnetic material that is sealed in a glass tube filled with inert gas. The end faces of the magnetic sheets overlap but there is a certain gap in the middle, and the end face contacts are plated with a layer of precious metals (such as rhodium, ruthenium, etc.). Increases the stability of the switch and extends the service life of the machine.
DOLAM ZP
Reed switch consists of an elastic reed of magnetic material that is sealed in a glass tube filled with inert gas. The end faces of the magnetic sheets overlap but there is a certain gap in the middle, and the end face contacts are plated with a layer of precious metals (such as rhodium, ruthenium, etc.). Increases the stability of the switch and extends the service life of the machine.
ALEPH HYR
Reed switch consists of an elastic reed of magnetic material that is sealed in a glass tube filled with inert gas. The end faces of the magnetic sheets overlap but there is a certain gap in the middle, and the end face contacts are plated with a layer of precious metals (such as rhodium, ruthenium, etc.). Increases the stability of the switch and extends the service life of the machine.
LITTELFUSE MDSR
Reed switches have contact types of normally open (Form A), normally closed (Form B) and normally closed normally open conversion (Form C). They are triggered by the magnetic field generated by a permanent magnet or a current-carrying coil.
- FAST Mall
- Cases
Smart Home
The company can provide professional high-voltage interconnection solutions for new energy vehicles.
Industrial Automation
Intelligent control and operation maintenance of the entire process of industrial manufacturing to improve production efficiency and quality, reduce energy consumption, and ensure production safety
Automotive Field
While you are still on your way, you can remotely turn on various household appliances, so that when you get home, a comfortable and warm indoor awaits you.
Smart Healthcare
The company can provide interconnection solutions such as mixed high and low frequency, mixed photoelectric, high life module connectors, and high voltage cable assemblies medical equipment.
Instruments Meters
In harsh conditions, carry out reliable data measurement, accurately predict machine failures, maintain equipment health, improve productivity, and reduce maintenance costs
Security Equipment
Security sensors are an indispensable part of safety monitoring systems. They can perceive changes in the surrounding environment and transmit this information to...
Semiconductor
The semiconductor machine is generally composed of a power system, developer tank and spray nozzle, washing tank, squeezing (water) roller, and coating tank. It is suitable for the surface development of semiconductor, chemical materials, silicon wafers,
Consumer Electronics
Capacitors, as one of the three basic passive electronic components (resistors, capacitors, and inductors), hold an important in the electronic component industry. They are mainly used for tuning, filtering, coupling, bypassing, and energy conversion in c
- Contact Us
- Mould Reed Switch
- MODEL Reed SwitchSIP Mould Reed Switch SeriesLine Mould Reed SwitchSMD Mould Reed Switch Series
- Reed Relay
- Reed RelayIndustrial Relay
- Proximity switch/sensor
- Magnetic Reed TypeHall TypeSCR/MOSFET TypeMagnetic Door TypePhotoelectric TypeInductive TypeDual-stable reed switch
- Float Switch/Sensor
- Plastic MaterialsStainless Steel SeriesPhotoelectric Liquid Level SensorProbe Level Sensor
- Liquid Level Sensor
- Continuous Resistance Change4-20mA Current output0-5V Voltage output
- Flow Switch
- Plastic Flow SwitchStainless Steel Flow SwitchBrass Flow SwitchGas/Air Flow Switch
- Flow Sensor
- Plastic Flow SensorStainless Steel Flow SensorBrass Flow SensorGas/Air Flow Sensor
- Pressure Switch
- Plastic Pressure SwitchBrass Pressure SwitchStainless Steel Pressure SwitchPressure Sensor
- Water Detection/Leak Sensor
- Probe Water Leak Detection SensorPhotoelectric Water Leak Sensor
- Tilt switch
- Tilt Switch / Ball Switch SensorCoal flow switchAngle Sensor
- Acceleration&Shock Switch
- Acceleration SwitchShock SwitchSpeed Switch
- Temperature Sensor
- Temperature switch sensorTemperature Sensor NTCTemperature Sensor-PT100
- Cylinder Magnetic Sensor
- Reed Type Cylinder Magnetic SensorHall Type Cylinder Magnetic Sensor
- Component Parts of Sensors
- Float BallHoured MagnetPCB PartsStainless steel parts
- Reed Switch
- COTO RICOMUS GCSTANDEX ORDDOLAM ZPALEPH HYRLITTELFUSE MDSR
- Smart Home
- Smart home solution
- Industrial Automation
- Industrial automation solution
- Automotive Field
- Automotive field solution
- Smart Healthcare
- Smart healthcare solution
- Instruments Meters
- Instrumentation Solutions
- Security Equipment
- Security surveillance solution
- Semiconductor
- Solutions for the semiconductor field
- Consumer Electronics
- Consumer electronics solutions
Products
PRODCTS
Products
PRODUCTS
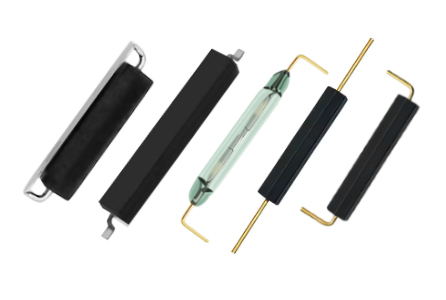
Mould Reed Switch
Built-in magnetic spring, quick alarm, convenient and easy to install, can be customized
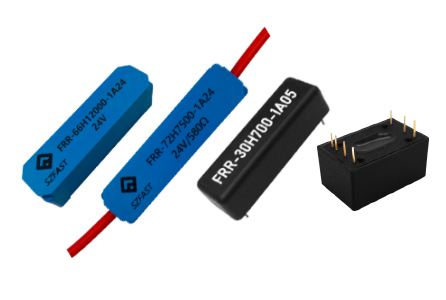
Reed Relay
High sensitivity, high reliability, strong applicability, stable performance and long life
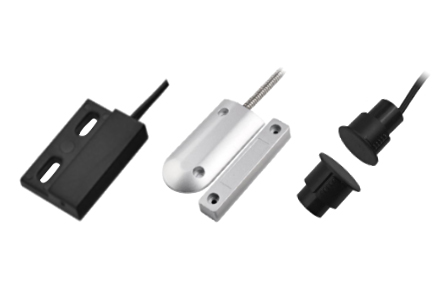
Proximity switch/sensor
Used for household appliances, sports equipment, automobiles, and industrial equipment, with high sensitivity and high repeatability accuracy.
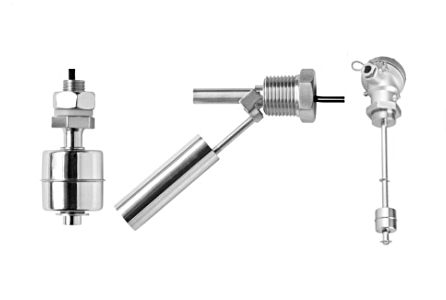
Float Switch/Sensor
Used in manufacturing/automotive industry/smart appliances, strong durability, customizable.
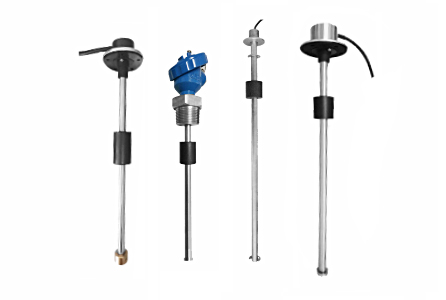
Liquid Level Sensor
Available in a variety of sizes, single ball single point, single ball multiple points, and hanging ball multiple points
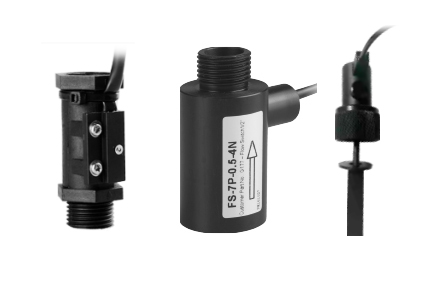
Flow Switch
Used in food production, refrigeration equipment, water purification treatment, power equipment, petrochemical industry, with excellent performance.
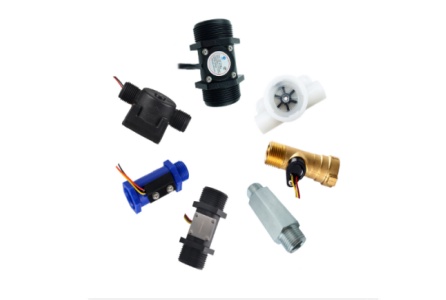
Flow Sensor
Flow sensors display and flow accumulation calculation. It can be used as a flow switch and also as a flow meter for flow accumulation calculation.
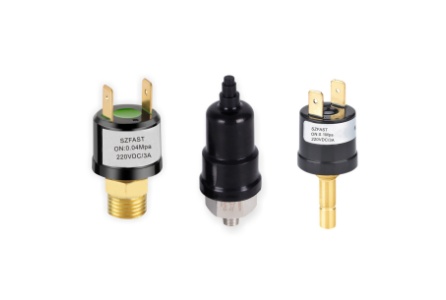
Pressure Switch
Applied in various industrial fields,
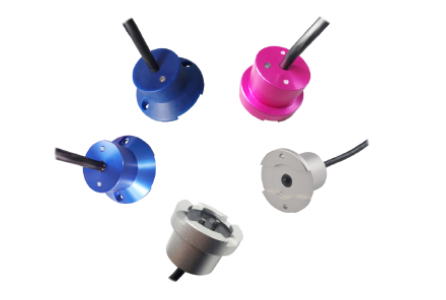
Water Detection/Leak Sensor
Fast detection speed, wide monitoring range, sensitive reaction, good durability, accurate positioning
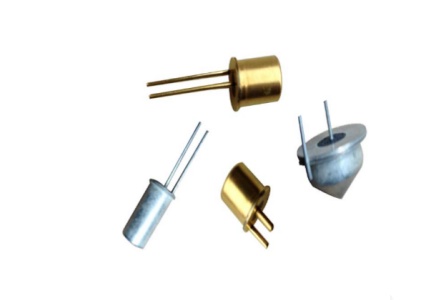
Tilt switch
Tilt switch is suitable for food, silica sand, rock, small particles, wood, soil, rubber, metal, processed materials, coal, mixed oil, soil, resin, limestone, particles, malt etc
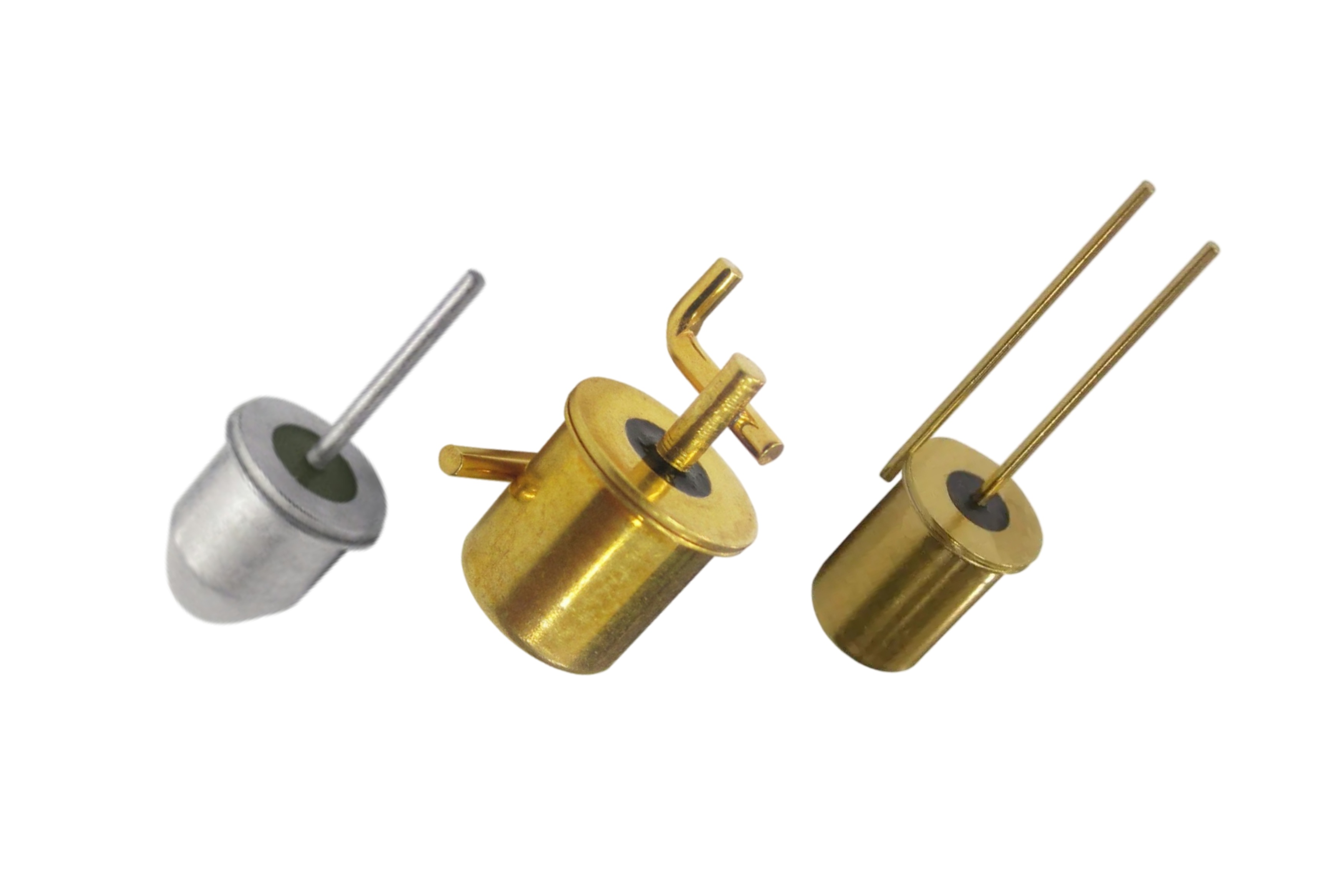
Acceleration&Shock Switch
The products can be integrated into various electronic devices and systems, durable, directional and fast response
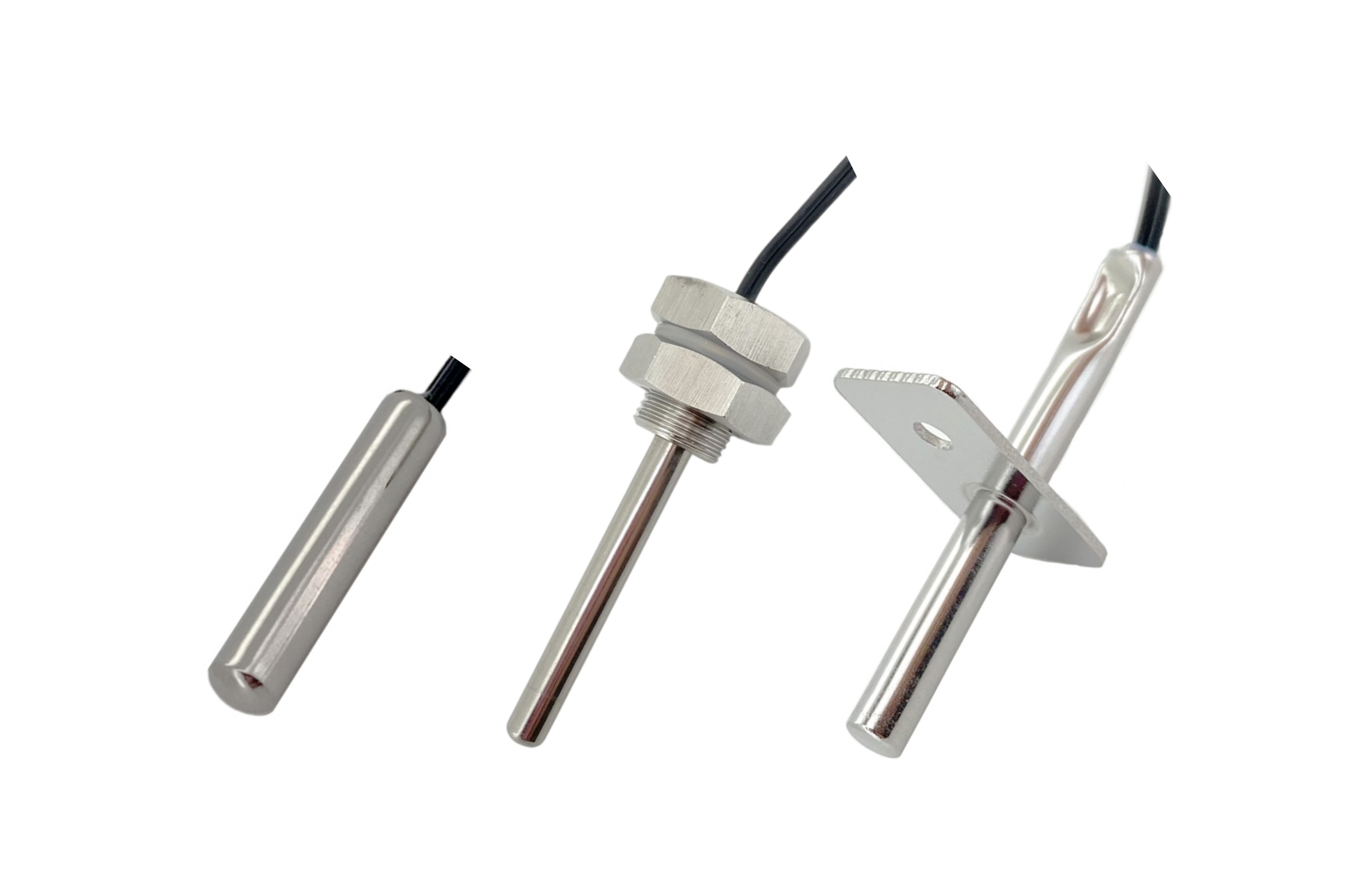
Temperature Sensor
High accuracy, high resolution, strong anti-interference, suitable for fast response or high-precision measurement scenarios
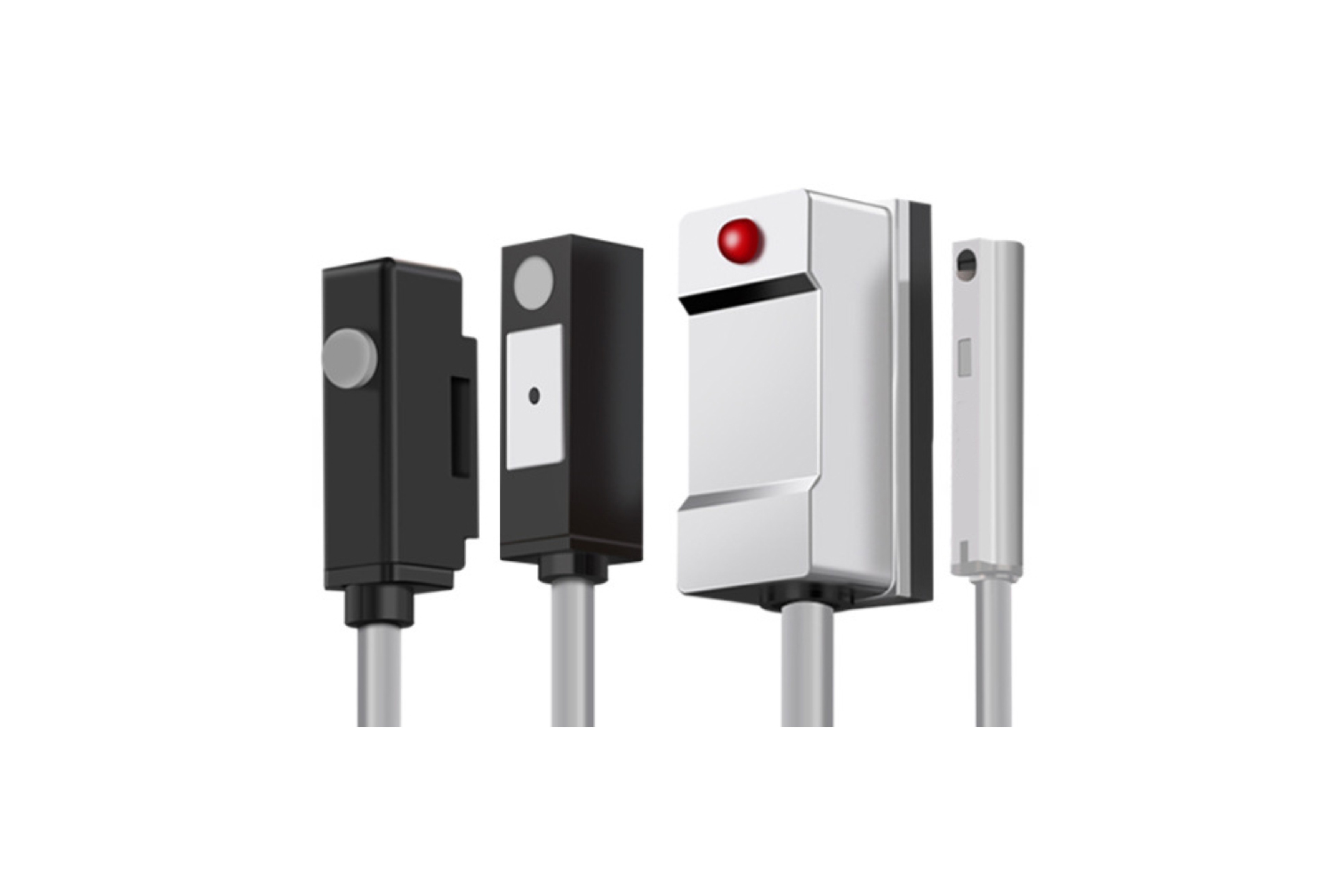
Cylinder Magnetic Sensor
Non-contact detection, high reliability, fast response speed, widely used in automatic control systems
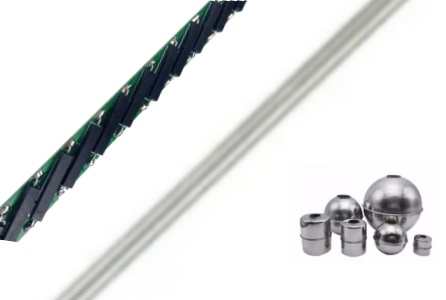
Component Parts of Sensors
Sensor components include floats, magnets, reed PCB components and kits made of different materials.
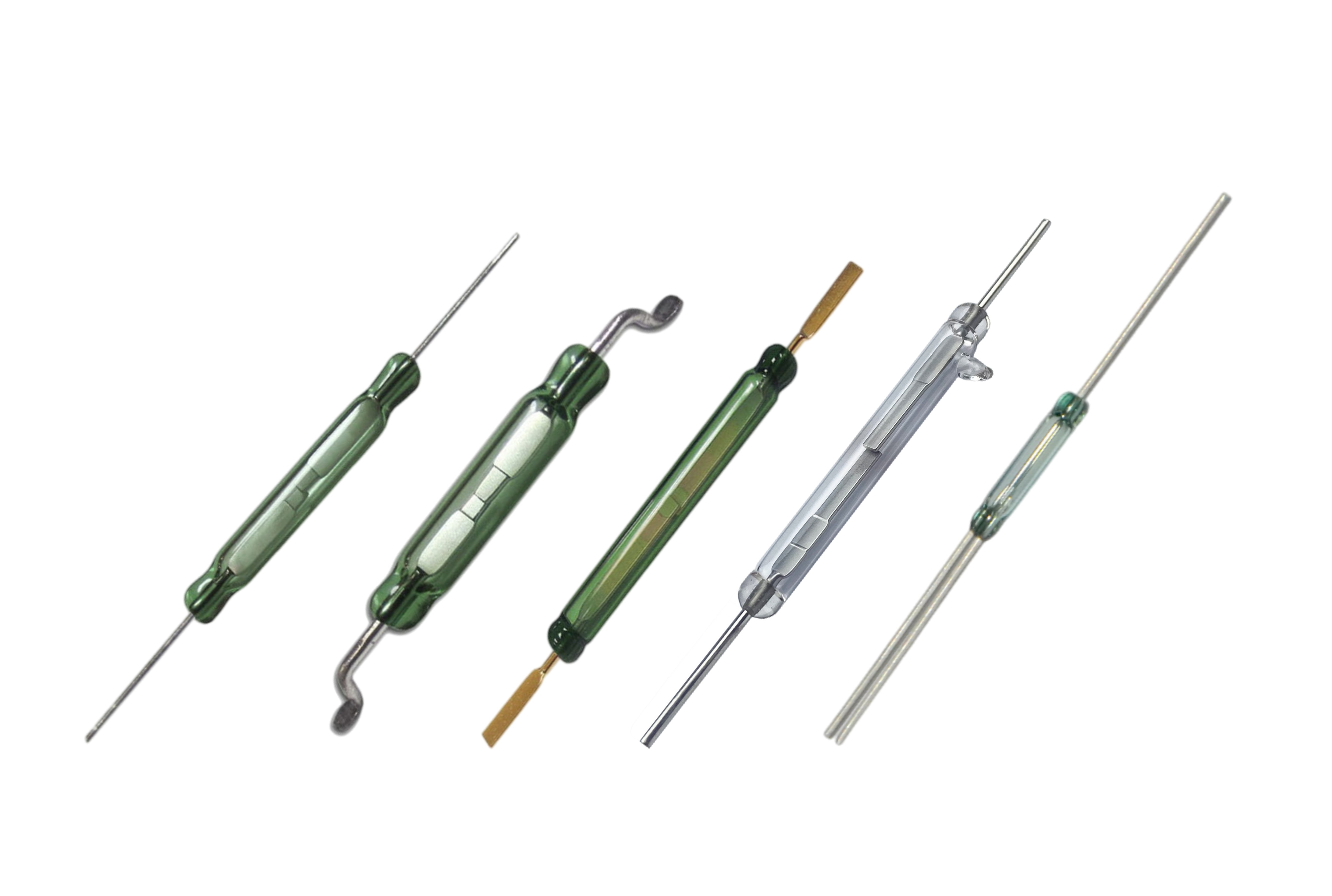
Reed Switch
Widely used in transistors and integrated circuits, it has a compact structure, light weight, and long lifespan.
FAST ELECTRIC LIMITED. Copyright © 2024 All Rights reserved.